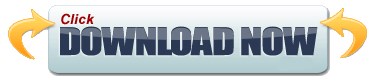

Its about money, paycheck, profits, and forget about the notion of 7 day weeks and evenings at home working on the books or takeoffs and designs. If i had, I would've likely given them my business by now and been sitting back in a shop/advisory position (hopefully on the shop floor getting dusty every day) taking a percentage lol.Įven my best people over the years are just not interested in anything regarding why I/we do what we do. Sadly, I havent had an individual in the shop in many many years (perhaps ever) that would land in the "cabinetmaker" realm in my eyes or even their own and I dont have unreasonably high standards. I completely understand the merits of your point, honest and truly I do. I agree it's simpler, but does it make better cabinet makers?
#Cutlist plus fx phone number software
With the software its just about seamless. That said, the scenario you mentioned of 1000's of parts, and a large percentage of them being unique, use to land me with a hefty pile of scraps, waste, mis-cuts, and so on. I will admit that once you get fully integrated with cutlisting out of software you (I know I do) can begin to get a little soft or less sharp than you were. Beyond that, even when I am cutting myself I still make random math errors, forget about an interference or some reason why I am running this one part different than the way I have run it hundreds of times before. Its rare to get even the best employees to engage at a level anywhere near that of the business owner. He can see 2 steps in front of him, but not 10-20.Ĭouldnt agree more. My helper will only cut what the sheet says. I have the mental ability to correct/adjust on the fly if a sheet is "weird" or I don't recognize a dimension (but I'm the guy designing from the ground up and integrating all my reports from cabinet vision to CLP). :D No doubt! I change or learn something every job. None of us are doing it right, that I'll bet on. The different priorities as to what to pour money into to reduce bottlenecks, and what different people focus on is equally fascinating. We cut those up like face frame material after ripping the needed lineal footage. Anything that is toe, nailer, stretcher or "unseen" material is left out of the program. Before every job I'll write down and input every off-cut per type of material I can use for that particular job. Most of what I like about the program is being able to input and use up all my off-cuts. If you hand us both the same cutlist sheet we'll break it down totally different - doesn't matter if the sheet is set for prefer "rip", "cross", "standard" or "max cutoff". He can see 2 steps in front of him, but not 10-20. Pencil and marking off a sheet works just fine for a 2 man shop.
#Cutlist plus fx phone number upgrade
It has the upgrade to input the size of the board to the nearest defect, but I'm not paying $2k for a thermal printer to get the labels printed with that method. Solid stock: I just use the TigerStop and biggest to smallest method. I like the added features of the Silver edition, but it might be one of those things where they sound a lot cooler and more useful than they actually would be for my use.įor me: CLP is the starting point for all my off-cuts and sheet goods. Hmmm, perhaps I will start with the basic version (cheapest) and see if I need/want anymore than that. If I had to build something with 60/70 different parts might be worth it Regarding the SketchUp link, am just dabbling with this but most projects I build, its quick to enter the parts into the list without a link.

Things I like about it - ease of use, quick to generate layouts, layouts can be tweaked based on different parameters (min waste, grain direction and so on), easy to put parts in, raw materials list is very flexible. It does have a lot of functions I don't use like costing and labor which are aimed at a business. Silver might be a bit excessive for me as a hobbyist but it was the cheaper upgrade from the old fx I used to have, so not a big deal. I've used CutList Plus Silver for a few years, Ben.
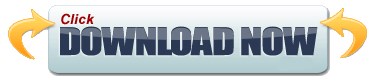